Preperation and Testing of Drilled Shafts with Self - Consolidating Concrete
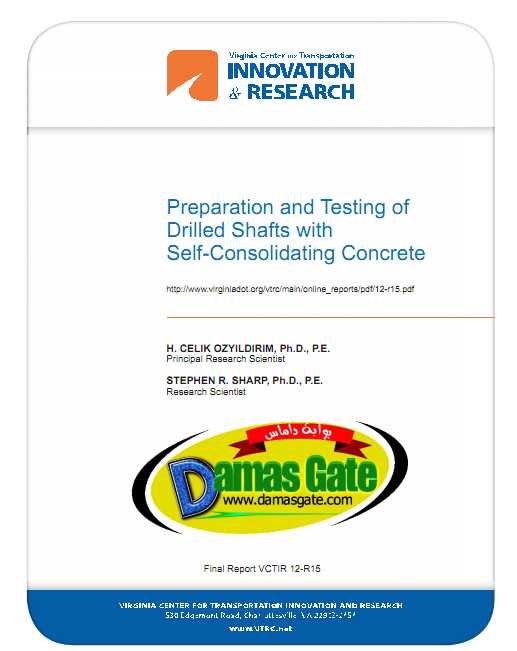
INTRODUCTION
A drilled shaft is a deep foundation that is constructed by placing fresh concrete in a drilled hole (Michael and Lymon, 1999). These massive shafts have diameters ranging from 18 in to 12 ft or more and contain a high concentration of reinforcement bars. Drill shafts offer economic advantages because pile caps are not necessary and the shafts tie directly into columns. A typical shaft is easily adaptable to varying site conditions and can carry a high load. Drilled shafts are not recommended for contaminated sites since contamination may spread within the site; other drawbacks include a lack of associated construction expertise, difficulty of concrete placement, and difficulty of inspecting the finished product.
Drilled shaft excavation requires either cased or uncased methods. If soils are not prone to caving, as with stiff clay, shale, or limestone, a casing is not required. Generally, bentonite slurry is used to support the sides of the hole and keep it from collapsing (Jalinoos et al., 2005). However, if soils are prone to caving, casings are used to support the sides of the excavation.
During placement by tremie or pump line, the discharge end is placed near the bottom of the hole and the concrete flow is started. The concrete fills the shaft from the bottom and displaces the sediments. The placement continues until fresh concrete overflows the top of the shaft. The concrete placed first rises to the surface; therefore, it is important to provide concrete that stays plastic until the placement is completed. Generally, concretes with high consistency (flowability) are placed, which can lead to bleeding and segregation. Consolidation of deep shafts is not practical, and the presence of large air pockets because of the lack of consolidation has been a concern.
In the past, the Virginia Department of Transportation (VDOT) permitted free fall into
the excavation of dry shafts up to 75 ft in depth. The new specifications being developed will allow free fall only with a drop chute and when approved by the Engineer. The maximum coarse aggregate size is reduced to 3/8 in from the commonly used size of 3/4 in. Concrete should be deposited without striking the reinforcement cage during free fall to minimize segregation. Accumulation of water at the base of excavation is also a concern because of voids and weak concrete at the bottom adversely affecting the bearing resistance.
Download
*