Repair and Rehabilitation of Bridge Components Containing Epoxy - Coated Reinforcement
INTRODUCTION AND RESEARCH APPROACH
NTRODUCTION
Early research by the National Bureau of Science (now National Institute of Standards and
Technology) and the Federal Highway Administration indicated that reinforcing bars that were
cleaned and then coated with select powdered epoxies using an electrostatic spray process
performed well in salt contaminated concrete (1). Such coated rebars were determined to be
resistant to corrosion, such that premature deterioration of concrete due to the pressures
generated by expansive corrosion products was minimized.
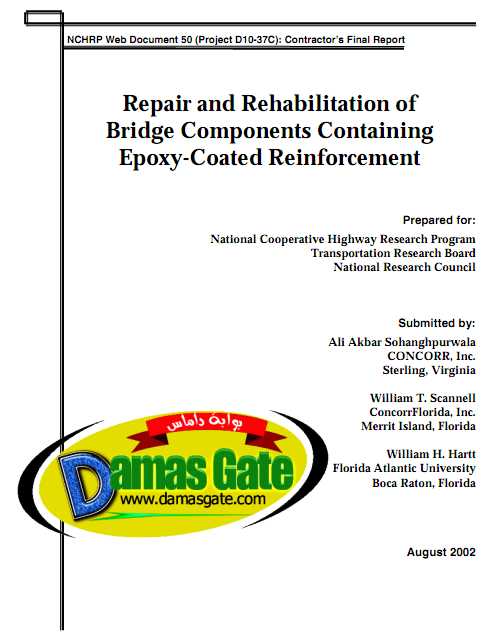
Epoxy resins are thermosetting poly-addition polymers and have, for the most part, been reported
to have good long-term durability in concrete and to be resistant to solvents, chemicals and water
(2). In addition, epoxy resins generally possess the necessary mechanical properties for such
service including good ductility, small shrinkage upon polymerization and good heat resistance
(3). Further, test results have indicated that the oxygen and chloride ion permeabilities of epoxy
coatings are relatively low, even in worst case exposures (1, 2, 4). Epoxy coatings are, on the
other hand, permeable to moisture (water); and it has been known for years, although not
highlighted within the highway community, that the adhesion of epoxy based coatings to steel is
reduced upon exposure to moisture (5). Thus, the fundamental attribute by which an epoxy
coating affords corrosion protection to substrate steel arises from its barrier nature which retards
ingress of chloride ions and oxygen. Also, by increasing the electrical resistance between
neighboring coated steel locations, these coatings reduce the magnitude of macroscopic
Download
http://s18.alxa.net/s18/srvs2/02/002...nforcement.rar