IronCAD Multiphysics 2019 v21.00
IronCAD recently announced the newest release of its Multiphysics for IronCAD (MPIC) finite element analysis (FEA) tool with several technologies added specifically for analyzing CAD assemblies.
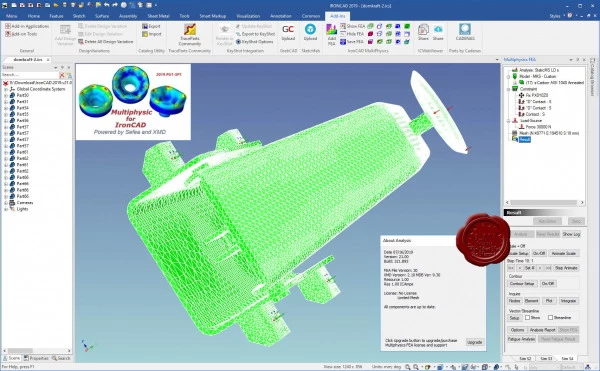
Multiphysics for IronCAD is an integrated multiphysics FEA simulation tool that works directly in the IronCAD interface. To use it, users simply add material, forces and constraints to an IRONCAD model and press the "Auto Solve” button to generate analysis results. If subsequent modifications are made to the model, associativity updates and re-solves the model. This free version has node limits and can be used for relatively small assemblies.
For an additional cost, the next step up for MPIC provides fully coupled multiphysics for stress, thermal and electrostatic analysis. Included at this level of the integrated multiphysics simulation software are the following analysis types: static/steady state, dynamic/transient response, modal/vibration modes, instability buckling and frequency domains.
For advanced and specialized users, MPIC can be augmented with optional add-ons. The Advanced package includes large deformation and large rotation features and can be used to model nonlinear elastic, plastic and foam materials. The Advanced Dynamic add-on includes stress stiffened modal and arc-length nonlinear buckling analysis. The Fluid package covers flow physics impact.
Highlights for the new MPIC release include:
New rigid body kinematic (RBK) capabilities that combine rigid body and finite element technologies for faster analysis. Parts needing critical accuracy are analyzed using Strain-Enriched FEA (SEFEA) multiphysics technology. SEFEA takes parts of finite element, boundary element and mesh-free technologies for general simulation accuracy and speed.
Non-crucial parts or connecting mechanisms are treated as rigid bodies for transmitting constraints, loads or motion for assembly analysis. Mechanism assemblies, gearing systems and camscan have complex motion. If you want to find the motion of a specific point in these systems, you will need to know how to use kinematics of a rigid body. Kinematics allow you to determine position, velocity and acceleration. After determining the acceleration, you can then use kinetics to determine forces. This chain of events can be complicated, but MPIC lessens the load with just a few relatively simple steps.
An updated user interface with an expandable/customizable material database of more than 500 types of material data.
Enhanced multithread controls that can take advantage of scalable CPUs for enhancing performance.
According to Chuck Paulsen, business director for AMPS Technologies, an IronCAD simulation development partner, the newest version of MPIC, "is a first in CAE applications to easily and seamlessly utilize both rigid and flex body formulations to analyze CAD assemblies quickly and accurately from early concept to final stage design.”
17.2MB
Download
http://s15.alxa.net/001/03/IronCAD.M...019.v21.00.rar
IronCAD recently announced the newest release of its Multiphysics for IronCAD (MPIC) finite element analysis (FEA) tool with several technologies added specifically for analyzing CAD assemblies.
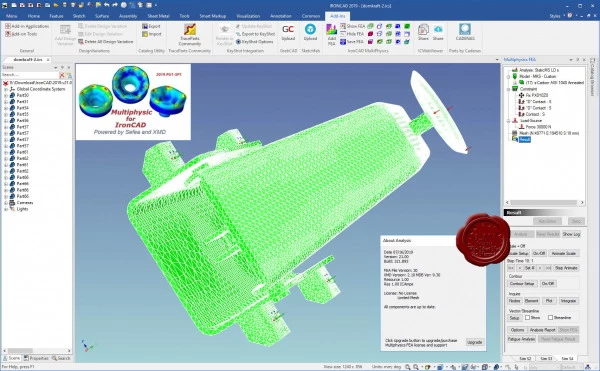
Multiphysics for IronCAD is an integrated multiphysics FEA simulation tool that works directly in the IronCAD interface. To use it, users simply add material, forces and constraints to an IRONCAD model and press the "Auto Solve” button to generate analysis results. If subsequent modifications are made to the model, associativity updates and re-solves the model. This free version has node limits and can be used for relatively small assemblies.
For an additional cost, the next step up for MPIC provides fully coupled multiphysics for stress, thermal and electrostatic analysis. Included at this level of the integrated multiphysics simulation software are the following analysis types: static/steady state, dynamic/transient response, modal/vibration modes, instability buckling and frequency domains.
For advanced and specialized users, MPIC can be augmented with optional add-ons. The Advanced package includes large deformation and large rotation features and can be used to model nonlinear elastic, plastic and foam materials. The Advanced Dynamic add-on includes stress stiffened modal and arc-length nonlinear buckling analysis. The Fluid package covers flow physics impact.
Highlights for the new MPIC release include:
New rigid body kinematic (RBK) capabilities that combine rigid body and finite element technologies for faster analysis. Parts needing critical accuracy are analyzed using Strain-Enriched FEA (SEFEA) multiphysics technology. SEFEA takes parts of finite element, boundary element and mesh-free technologies for general simulation accuracy and speed.
Non-crucial parts or connecting mechanisms are treated as rigid bodies for transmitting constraints, loads or motion for assembly analysis. Mechanism assemblies, gearing systems and camscan have complex motion. If you want to find the motion of a specific point in these systems, you will need to know how to use kinematics of a rigid body. Kinematics allow you to determine position, velocity and acceleration. After determining the acceleration, you can then use kinetics to determine forces. This chain of events can be complicated, but MPIC lessens the load with just a few relatively simple steps.
An updated user interface with an expandable/customizable material database of more than 500 types of material data.
Enhanced multithread controls that can take advantage of scalable CPUs for enhancing performance.
According to Chuck Paulsen, business director for AMPS Technologies, an IronCAD simulation development partner, the newest version of MPIC, "is a first in CAE applications to easily and seamlessly utilize both rigid and flex body formulations to analyze CAD assemblies quickly and accurately from early concept to final stage design.”
17.2MB
Download
http://s15.alxa.net/001/03/IronCAD.M...019.v21.00.rar