Siemens Simcenter MotorSolve 2021.1.0 x64
Siemens Digital Industries Software announced releases of Siemens Simcenter MAGNET software and Simcenter Motorsolve software for simulating electric motor design and electromagnetic fields at any stage of the design process. Electric traction motors must be durable and NVH-compliant, however, electromagnetic forces induce mechanical vibrations which may lead to failure.
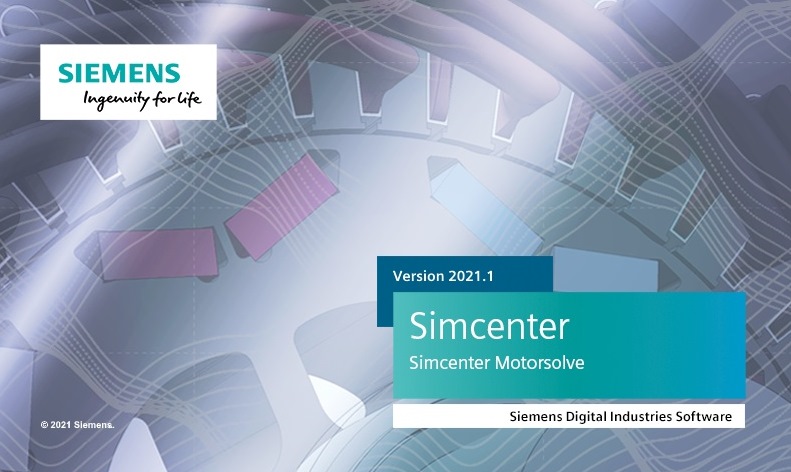
The Simcenter MAGNET and Simcenter Motorsolve solution calculates the behavior of electromagnetic forces on individual components, providing examination of the structure and materials integrities under multiple operating conditions during any phase of the design process. These capabilities are important for implementing a realistic digital twin of electric and hybrid electric vehicle powertrains or for any application where NVH constraints are critical, such as aerospace, industrial and medical equipment.
Siemens’ approach to NVH analysis is unique since the Simcenter Motorsolve tool uses smart 2.5D technology to generate a 3D nodal force mesh model based on 2D simulations. Net forces on components can be determined using Simcenter MAGNET software, even when they are in contact, including artificial component grouping. Simcenter SPEED PC-BDC models can be imported into Simcenter Motorsolve software for higher-resolution finite element simulations, and Simcenter 3D electromagnetic software integration can provide electric motor simulation performance. Now, design engineers can apply a range of real-world conditions in their electro-vibro-acoustic simulation analysis.
Motor and generator designers can use this software for quick virtual prototyping.
MotorSolve simulates machine performance using equivalent circuit calculations and our unique automated finite element analysis engine. Typical FEA operations, such as mesh refinements and post-processing, are not required as MotorSolve handles these for the user.
The template-based interface is easy to use and flexible enough to handle practically any motor topology. Custom rotors and stators can be imported via DXF.
File Size: 520.5 MB
Siemens Digital Industries Software announced releases of Siemens Simcenter MAGNET software and Simcenter Motorsolve software for simulating electric motor design and electromagnetic fields at any stage of the design process. Electric traction motors must be durable and NVH-compliant, however, electromagnetic forces induce mechanical vibrations which may lead to failure.
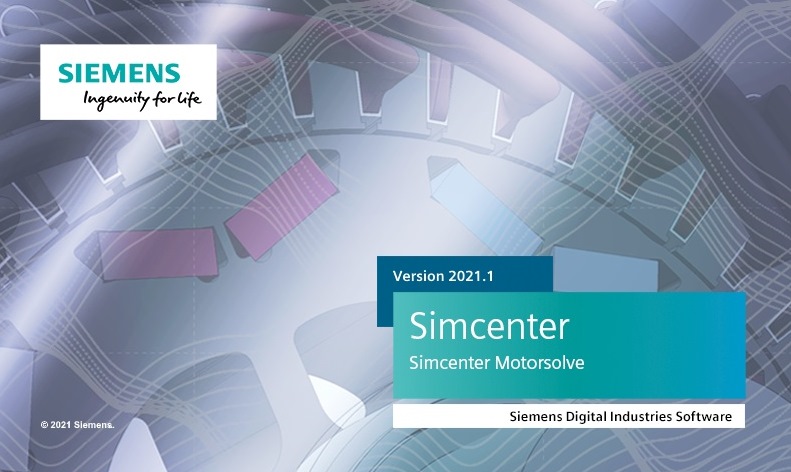
The Simcenter MAGNET and Simcenter Motorsolve solution calculates the behavior of electromagnetic forces on individual components, providing examination of the structure and materials integrities under multiple operating conditions during any phase of the design process. These capabilities are important for implementing a realistic digital twin of electric and hybrid electric vehicle powertrains or for any application where NVH constraints are critical, such as aerospace, industrial and medical equipment.
Siemens’ approach to NVH analysis is unique since the Simcenter Motorsolve tool uses smart 2.5D technology to generate a 3D nodal force mesh model based on 2D simulations. Net forces on components can be determined using Simcenter MAGNET software, even when they are in contact, including artificial component grouping. Simcenter SPEED PC-BDC models can be imported into Simcenter Motorsolve software for higher-resolution finite element simulations, and Simcenter 3D electromagnetic software integration can provide electric motor simulation performance. Now, design engineers can apply a range of real-world conditions in their electro-vibro-acoustic simulation analysis.
Motor and generator designers can use this software for quick virtual prototyping.
MotorSolve simulates machine performance using equivalent circuit calculations and our unique automated finite element analysis engine. Typical FEA operations, such as mesh refinements and post-processing, are not required as MotorSolve handles these for the user.
The template-based interface is easy to use and flexible enough to handle practically any motor topology. Custom rotors and stators can be imported via DXF.
File Size: 520.5 MB