Altair Inspire Mold 2024.1 (x64)
Injection Molding Simulation.
Injection molding of plastics is an established, proven industrial manufacturing process for the mass production of identical components. Inspire Mold provides a modern integrated approach to streamline design for manufacturing (DfM) of injection molded components. Simulation is finally democratized and placed in the hands of designers and product engineers early in the development cycle, enabling easy exploration of options and delivering improved products, reduced scrap, and tooling rework costs.
Understand how the mold fills with a fast analysis, then dig deeper into the process with a detailed simulation of all the advanced physics.
Virtual testing, validation, correction, and optimization of molding designs can be easily performed through a five-step workflow, providing access to evaluation of injection molded part manufacturability that mitigates common manufacturing defects (warping, sink marks, short shots, etc.) long before a mold is made.
Altair offers a comprehensive set of solutions to develop innovative, manufacturable products faster: from the initial design of the part and understanding the injection molding process, to material mapping of reinforced engineering polymers and efficiently analyzing and optimizing the structural and fatigue performance of complex parts.
Why Inspire Mold?
Reduce Product Development Costs
Identifying manufacturing defects early in the development process reduces costly mold trials and reject rates.
Make Better Product Design Decisions Early
Faster more informed product design cycles, with fewer iterations lead to the development of better, structurally efficient, and manufacturable parts.
Deliver Production-ready Tools on Time and on Budget
Transition from "know how" to "know why," assessing product feasibility when changes can still be made through a simple five-step process.
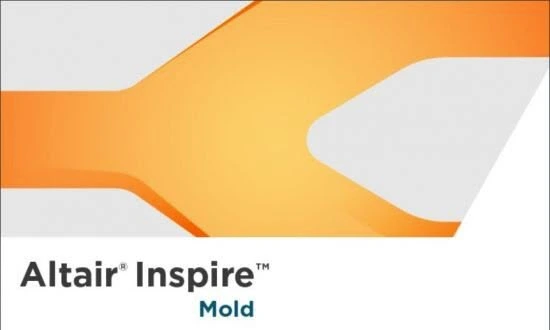
File size: 4.9 GB
Download
Injection Molding Simulation.
Injection molding of plastics is an established, proven industrial manufacturing process for the mass production of identical components. Inspire Mold provides a modern integrated approach to streamline design for manufacturing (DfM) of injection molded components. Simulation is finally democratized and placed in the hands of designers and product engineers early in the development cycle, enabling easy exploration of options and delivering improved products, reduced scrap, and tooling rework costs.
Understand how the mold fills with a fast analysis, then dig deeper into the process with a detailed simulation of all the advanced physics.
Virtual testing, validation, correction, and optimization of molding designs can be easily performed through a five-step workflow, providing access to evaluation of injection molded part manufacturability that mitigates common manufacturing defects (warping, sink marks, short shots, etc.) long before a mold is made.
Altair offers a comprehensive set of solutions to develop innovative, manufacturable products faster: from the initial design of the part and understanding the injection molding process, to material mapping of reinforced engineering polymers and efficiently analyzing and optimizing the structural and fatigue performance of complex parts.
Why Inspire Mold?
Reduce Product Development Costs
Identifying manufacturing defects early in the development process reduces costly mold trials and reject rates.
Make Better Product Design Decisions Early
Faster more informed product design cycles, with fewer iterations lead to the development of better, structurally efficient, and manufacturable parts.
Deliver Production-ready Tools on Time and on Budget
Transition from "know how" to "know why," assessing product feasibility when changes can still be made through a simple five-step process.
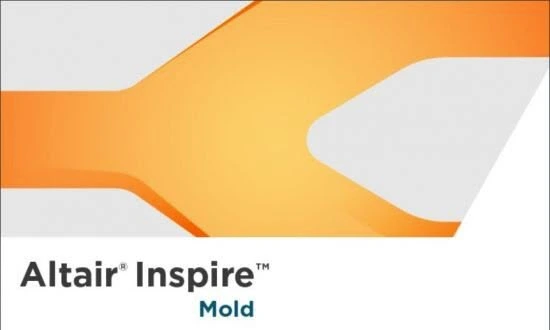
File size: 4.9 GB
Download