DS SIMULIA Suite 2024 (Abaqus/Isight/Fe-safe/Tosca) Win+Linux x64 [2024, ENG]
Finite Element Analysis (FEA) reaches the desk of the engineering analyst as a software package. Unless that software has been designed to exploit the true generality of the method, the analyst will become frustrated by the gap between the method's theoretical potential and the unnecessary limitations imposed by the software. This is where Abaqus shines. Abaqus is truly a general-purpose finite element-based software package.
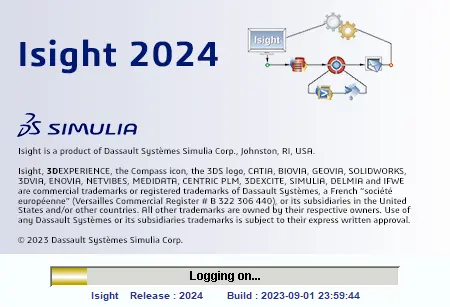
With an extensive library of element types, it can model nearly any geometry. Abaqus has an equally extensive library of material models that can simulate stress and deformation in isotropic and anisotropic metals at low and high temperatures, at low and high strain rates, and at small and large strains. Beyond metals, Abaqus can simulate rubber and polymers, reinforced concrete, glass and ceramics, crushable or resilient foam, and geotechnical materials like soils and rock.
However, Abaqus offers more than just stress analysis. With Abaqus, you can simulate conductive and convective heat transfer, mass diffusion, acoustics, piezoelectricity, and electrochemistry either independently, sequentially coupled, or fully coupled with the stress analysis. What makes Abaqus uniquely powerful is its modularity. You can model any physically reasonable combination of elements, materials, procedures, and loading sequences. Any material can be used with virtually any element (or, in the case of composites, in a layer of an element) and thus form a part of a model subjected to any sequence of static or dynamic loading histories.
Finite element simulation of large models
The need for a detailed understanding of designs increases with the complexity of those designs. This in turn leads to the requirement for large simulation models. The FEA system must allow the analyst to run very large problems easily while efficiently leveraging available computer resources. Abaqus takes advantage of the high-performance features of modern computers, so model size limitations rarely prevent you from realizing an adequate simulation. Users appreciate being able to meet schedules because the code runs large, complex jobs through to completion. Realistic models quickly expose how well the code’s designers took care of the details. Abaqus holds up under the rigors of real-life, large model requirements.
Simulation of nonlinearity
More and more frequently, the analyst must consider nonlinear response as an essential part of a simulation. Lightweight structures buckle; in accident scenarios, they may collapse. Some important modern materials — like rubbers and plastics — are too soft to simulate based on linearized deformation. Often the designer wishes to take full advantage of the ductility and toughness of the materials available. Many design problems involve contact, from Hertz contact in bearing design to general sliding contact between a part and the die or mold used to form it, or between two parts, each undergoing substantial deformation. Abaqus has been designed from its beginning to address these types of problems. This has led to its worldwide reputation as the tool of choice for simulations where nonlinearity dominates the response.
Simplicity of use in complex problems
The popularity of Abaqus as an advanced analysis code is based on its focus on production analysis. Despite its great breadth of capabilities, Abaqus is easy to learn and use. Because it is modular and has simple, consistent, and intuitive problem definition rules, you are freed from artificial and frustrating limitations. You can model geometry as closely as needed, define material behaviors associated with the various components of the model, and simulate a sequence of events of concern. At no time will the code limit this process unnecessarily. As far as possible, Abaqus relieves you of difficult tasks. One of the best examples is automatic time stepping in nonlinear static, dynamic, and heat transfer problems: Abaqus chooses and continuously adjusts the time increments automatically. This feature alone has permitted many users to perform simulations that would have been impossible otherwise. You can tackle realistic simulations with confidence of success and with the assurance of meeting design schedules.
Research organizations use Abaqus extensively because of its versatility and user-defined extensibility. But its great success has been built on its acceptance in the design analysis community as a general analysis tool that not only provides convenience in routine simulations but greatly extends the range of possible simulations.
What distinguishes Abaqus is its proven record of success in the largest and most complex problems. If you face relatively straightforward applications, you will find Abaqus a pleasure to use. If you are facing very challenging problems, you will come to rely on Abaqus as the one tool that provides reliable answers.
Abaqus/Standard
-Abaqus/Standard is ideally suited for static, low-speed dynamic, and steady-state transport applications.It enables analyses of a model in both time and frequency domain in one single simulation. Abaqus/Standard delivers highly accurate stress analyses.
-Abaqus /Standard can provide starting points for Abaqus/Explicit simulations as well as continuing from Abaqus/Explicit results. Pre- and postprocessing is supported within the Abaqus/CAE modeling environment.
Abaqus/Explicit
Abaqus/Explicit enables the simulation of brief transient dynamic events, such as drop testing or ballistic events with finite element analysis. Its ability to handle severely non-linear behavior makes Abaqus/Explicit ideally suited for the simulation of quasi-static events such as slow crushing of energy absorbing devices.
Abaqus/CAE
With Abaqus/CAE you can quickly and efficiently create, edit, monitor, diagnose, and visualize advanced Abaqus analyses. It supports interactive computer-aided engineering concepts such as feature-based, parametric modeling, interactive and scripted operation. Besides the built-in geometry creation it enables interfacing with other CAD environments for geometry and mesh imports or model synchronization. Abaqus/CAE also offers comprehensive visualization options, which enable users to interpret and communicate the results of any Abaqus analysis.
System Requirements
OS:Server 2008 R2 SP1 / Windows 8.1 / Server 2012 R2 / Windows 10
Minimum requirement
CPU:Intel x86-64processor
Memory:16GB RAM
GPU:100% OpenGL compatible graphics card
Storage:30GB of free disk space
High end server/ workstation recommendation
CPU:Dual Intel Xeon Scalable (also known as “Skylake” ) processor
Memory:32– 64 GB per CPU
GPU:NVIDIA Quadro series card dedicated to CAD/CAE applications
Storage:At least 500GB hard disk drive/SSDs may be used, but are not necessary for good simulation performance
Download
x64 | File Size: 19.37 GB
Finite Element Analysis (FEA) reaches the desk of the engineering analyst as a software package. Unless that software has been designed to exploit the true generality of the method, the analyst will become frustrated by the gap between the method's theoretical potential and the unnecessary limitations imposed by the software. This is where Abaqus shines. Abaqus is truly a general-purpose finite element-based software package.
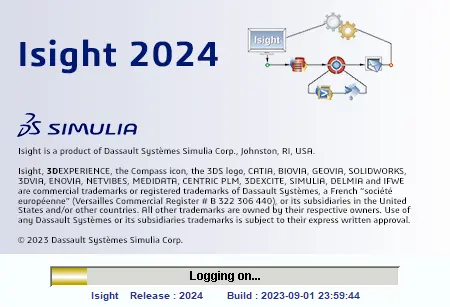
With an extensive library of element types, it can model nearly any geometry. Abaqus has an equally extensive library of material models that can simulate stress and deformation in isotropic and anisotropic metals at low and high temperatures, at low and high strain rates, and at small and large strains. Beyond metals, Abaqus can simulate rubber and polymers, reinforced concrete, glass and ceramics, crushable or resilient foam, and geotechnical materials like soils and rock.
However, Abaqus offers more than just stress analysis. With Abaqus, you can simulate conductive and convective heat transfer, mass diffusion, acoustics, piezoelectricity, and electrochemistry either independently, sequentially coupled, or fully coupled with the stress analysis. What makes Abaqus uniquely powerful is its modularity. You can model any physically reasonable combination of elements, materials, procedures, and loading sequences. Any material can be used with virtually any element (or, in the case of composites, in a layer of an element) and thus form a part of a model subjected to any sequence of static or dynamic loading histories.
Finite element simulation of large models
The need for a detailed understanding of designs increases with the complexity of those designs. This in turn leads to the requirement for large simulation models. The FEA system must allow the analyst to run very large problems easily while efficiently leveraging available computer resources. Abaqus takes advantage of the high-performance features of modern computers, so model size limitations rarely prevent you from realizing an adequate simulation. Users appreciate being able to meet schedules because the code runs large, complex jobs through to completion. Realistic models quickly expose how well the code’s designers took care of the details. Abaqus holds up under the rigors of real-life, large model requirements.
Simulation of nonlinearity
More and more frequently, the analyst must consider nonlinear response as an essential part of a simulation. Lightweight structures buckle; in accident scenarios, they may collapse. Some important modern materials — like rubbers and plastics — are too soft to simulate based on linearized deformation. Often the designer wishes to take full advantage of the ductility and toughness of the materials available. Many design problems involve contact, from Hertz contact in bearing design to general sliding contact between a part and the die or mold used to form it, or between two parts, each undergoing substantial deformation. Abaqus has been designed from its beginning to address these types of problems. This has led to its worldwide reputation as the tool of choice for simulations where nonlinearity dominates the response.
Simplicity of use in complex problems
The popularity of Abaqus as an advanced analysis code is based on its focus on production analysis. Despite its great breadth of capabilities, Abaqus is easy to learn and use. Because it is modular and has simple, consistent, and intuitive problem definition rules, you are freed from artificial and frustrating limitations. You can model geometry as closely as needed, define material behaviors associated with the various components of the model, and simulate a sequence of events of concern. At no time will the code limit this process unnecessarily. As far as possible, Abaqus relieves you of difficult tasks. One of the best examples is automatic time stepping in nonlinear static, dynamic, and heat transfer problems: Abaqus chooses and continuously adjusts the time increments automatically. This feature alone has permitted many users to perform simulations that would have been impossible otherwise. You can tackle realistic simulations with confidence of success and with the assurance of meeting design schedules.
Research organizations use Abaqus extensively because of its versatility and user-defined extensibility. But its great success has been built on its acceptance in the design analysis community as a general analysis tool that not only provides convenience in routine simulations but greatly extends the range of possible simulations.
What distinguishes Abaqus is its proven record of success in the largest and most complex problems. If you face relatively straightforward applications, you will find Abaqus a pleasure to use. If you are facing very challenging problems, you will come to rely on Abaqus as the one tool that provides reliable answers.
Abaqus/Standard
-Abaqus/Standard is ideally suited for static, low-speed dynamic, and steady-state transport applications.It enables analyses of a model in both time and frequency domain in one single simulation. Abaqus/Standard delivers highly accurate stress analyses.
-Abaqus /Standard can provide starting points for Abaqus/Explicit simulations as well as continuing from Abaqus/Explicit results. Pre- and postprocessing is supported within the Abaqus/CAE modeling environment.
Abaqus/Explicit
Abaqus/Explicit enables the simulation of brief transient dynamic events, such as drop testing or ballistic events with finite element analysis. Its ability to handle severely non-linear behavior makes Abaqus/Explicit ideally suited for the simulation of quasi-static events such as slow crushing of energy absorbing devices.
Abaqus/CAE
With Abaqus/CAE you can quickly and efficiently create, edit, monitor, diagnose, and visualize advanced Abaqus analyses. It supports interactive computer-aided engineering concepts such as feature-based, parametric modeling, interactive and scripted operation. Besides the built-in geometry creation it enables interfacing with other CAD environments for geometry and mesh imports or model synchronization. Abaqus/CAE also offers comprehensive visualization options, which enable users to interpret and communicate the results of any Abaqus analysis.
System Requirements
OS:Server 2008 R2 SP1 / Windows 8.1 / Server 2012 R2 / Windows 10
Minimum requirement
CPU:Intel x86-64processor
Memory:16GB RAM
GPU:100% OpenGL compatible graphics card
Storage:30GB of free disk space
High end server/ workstation recommendation
CPU:Dual Intel Xeon Scalable (also known as “Skylake” ) processor
Memory:32– 64 GB per CPU
GPU:NVIDIA Quadro series card dedicated to CAD/CAE applications
Storage:At least 500GB hard disk drive/SSDs may be used, but are not necessary for good simulation performance
Download
x64 | File Size: 19.37 GB